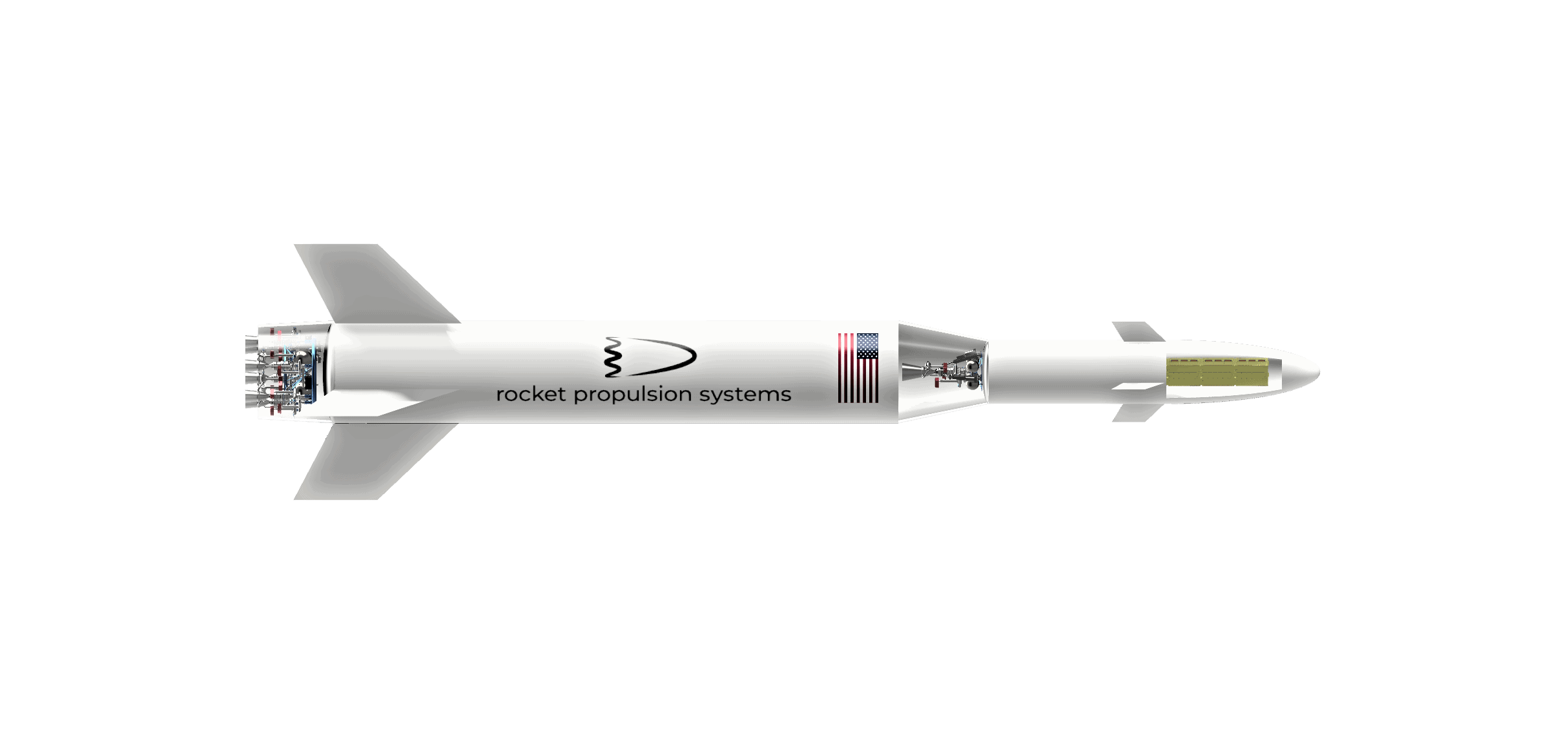
Engines
Do you need rocket engines for your small satellite launch vehicle?
- Price
- Centurion prototype specifications
- Architectural reasoning
- Engine variants
- Why not kerosene or hydrogen?
- What’s next in engine development?
Price
We built the first prototype of the Centurion rocket engine in October 2022. The prototype engine is planned to be commercialized in sea-level and vacuum variants. Both variants will feature a common core prototype technology, with the difference in nozzle extensions and clustering. The engines are intended to be used on small ground launched vehicles carrying small satellites to LEO or on in-space stages performing missions from LEO parking orbit to MEO/GEO, Moon, Mars and beyond, as described in Small Launch. The engines will be sold at a target price of $150K/engine – regardless of the variant – on U.S. and Canada markets. This low of an engine price is achieved via innovative exploitation of fuel-richness of the engine cycle, clever use of additive manufacturing and implementation of novel combustion device technologies. This low price point for propulsion is what is needed to offer a competitive launch to dedicated orbit at a price point of $1.5M (or $8300/kg, assuming a payload of 180 kg), if you want to go up against the commonly chosen ride share to suboptimal orbit.
Centurion prototype specifications
Centurion prototype engine was built to the high-level specifications shown in the table below. The prototype has a nozzle area expansion ratio of 12 and is regeneratively cooled down to the nozzle exit. The fielded engines will be elongated to larger nozzle area expansion ratios than the prototype via uncooled nozzle extensions.
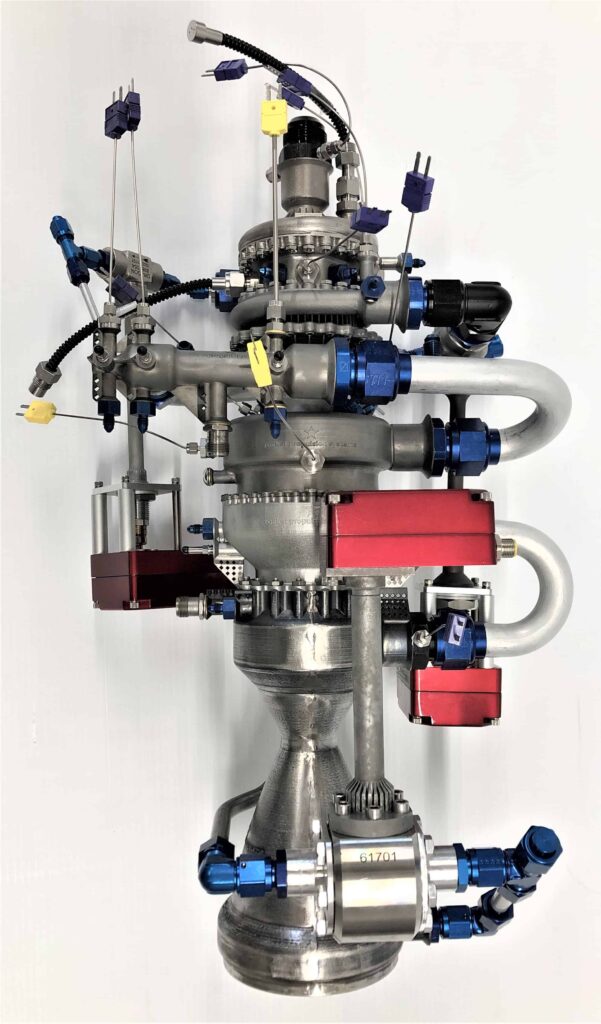
Oxidizer | Liquid oxygen (LOX) |
Fuel | Liquid methane (or Liquified Natural Gas) |
Cycle | Fuel-rich staged combustion |
Combustion chamber pressure | 103 bar [1500 psi] |
Specific impulse | 316 sec |
Thrust | 1.5 metric ton [3307 lbf] |
Dry weight | 15 kg [33 lbm] |
Nozzle area expansion ratio | 12 |
Envelope | 0.36 m [14 inch] diameter 0.61 m [24 inch] height |
Architectural reasoning
The engine features a fuel-rich staged combustion cycle on liquid oxygen (LOX)/methane propellants. LOX/methane are considered the propellants of future space flight spanning LEO-GEO near-Earth domain, and lunar and Martian missions, due to their wide availability and low cost on Earth, superior deep-space storability and potential for sourcing on Mars. The fuel-richness of the combustion cycle has been deliberately pursued in Centurion engine because of its historical reliability demonstrated in man-rated engines, such as XLR-99, F-1, Space Shuttle Main Engine, and Merlin. This reliability will convert into high rate of reusability in fielded engines. High chamber pressure has been targeted to allow for future upgrades in size and thrust without significant changes in thrust -to-weight ratio.
Engine variants
Exact engine specifications, such as launch vehicle / spacecraft interfaces, nozzle area expansion ratio and total thrust are to be determined with a specific customer. Below illustrations show an example of what we would expect to be typically offered for a small launch vehicle. The per-unit price for new engines and thrust-to-weight for both sea-level and vacuum variants are expected to remain close to $150K and 100:1 respectively. Because the engines are designed to be reusable – in a scenario when the 1st stage engines have successfully landed back on Earth and given back to RPS for refurbishing – the reused engines are targeted to be sold at 1/6 of a price of new engines. No reuse is anticipated for vacuum engines.
Boost Propulsion Module
Total price (all new engines) | $900K |
Total price (all reused engines) | $150K |
Number of engines | 6 |
Total thrust | 9 metric ton |
Specific impulse (sea level) | 332 |
Nozzle area expansion ratio | 20 |
Dry weight | 90 kg |
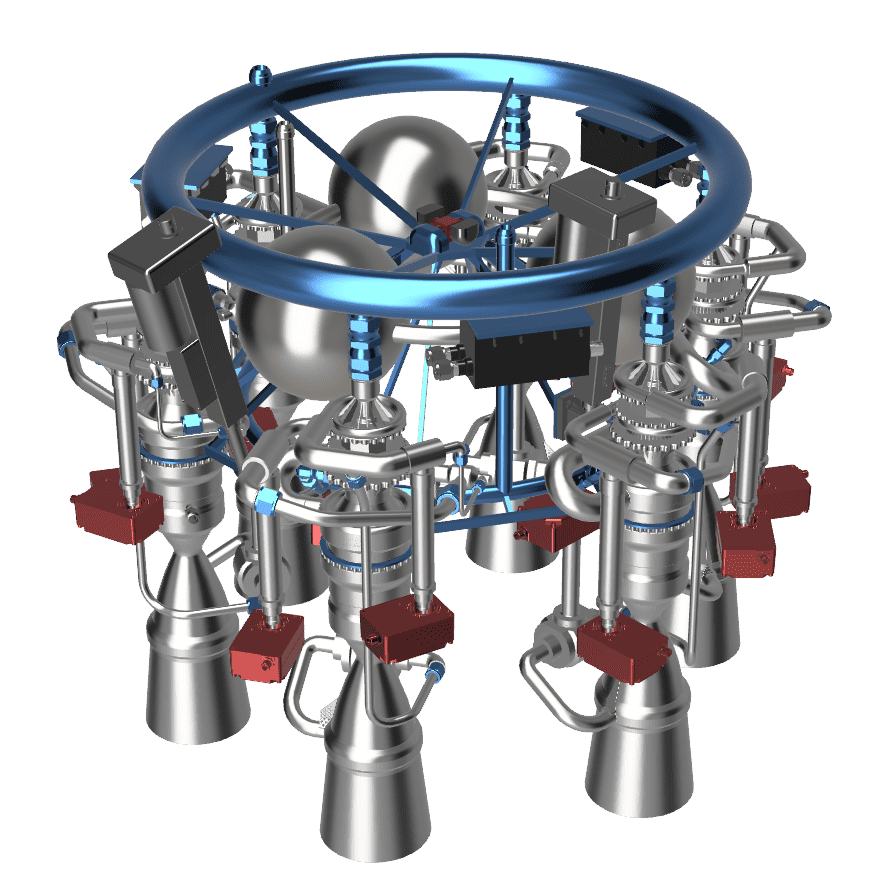
Vacuum / IN-SPACE Propulsion Module
Total price | $150K |
Number of engines | 1 |
Total thrust | 1.5 metric ton |
Specific impulse | 374 |
Nozzle area expansion ratio | 40 |
Dry weight | 15 kg |
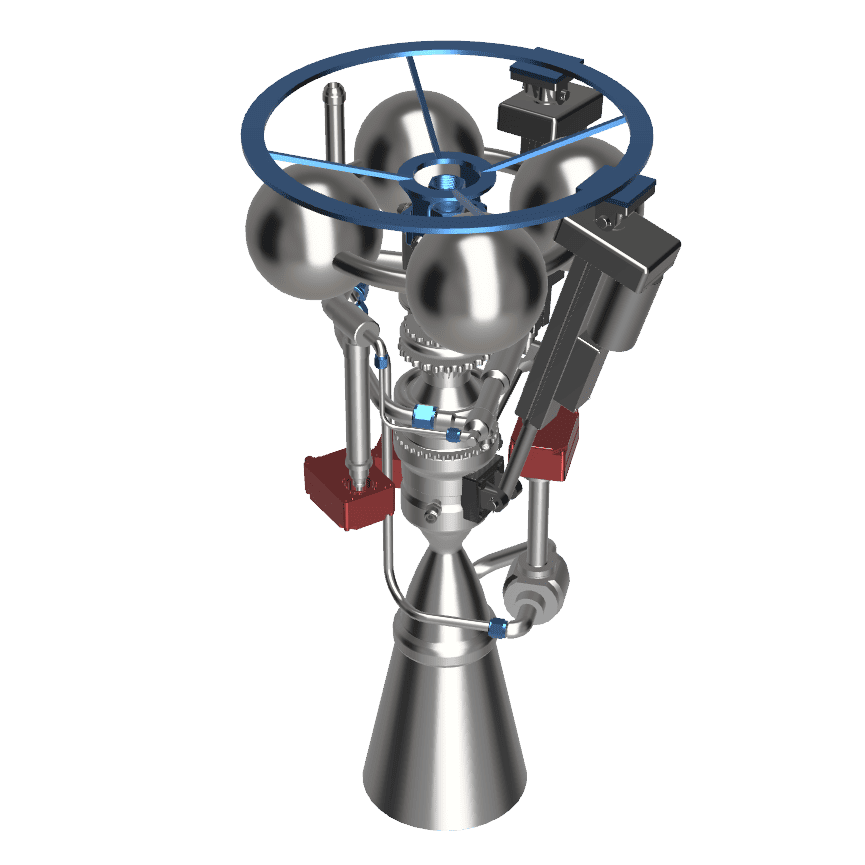
Why not kerosene or hydrogen?
We want to make truly affordable rocket engines so that people can build truly affordable rockets using them, and choice of fuel was considered deliberately in light of minimization of costs like engine development, operations, flight maintenance. Kerosene and hydrogen self-eliminated as described below, leaving methane as fuel of choice for Centurion.
Not Kerosene
Refined kerosene used to be the fuel of choice from World War 2 to Apollo, roughly. This fuel is produced abundantly on Earth, often on the same refineries that make gasoline for cars and jet fuel for aircraft – the cost of fuel is not an issue. However, when it comes to pump-fed rocket engines (the type of engines that gets the rockets to orbit), kerosene’s property to disintegrate at high temperatures becomes a problem in fuel-rich cycles. The fuel-rich cycles based on kerosene tend to clog up the turbines and thrust chamber cooling passages with soot, which may cause the engine to lose power over the course of its flight. This has led some designers to bias towards the oxidizer-rich cycles, where the liquid oxygen is preburned instead of kerosene – a preferred choice in Soviet-era kerosene engines. But the oxidizer-rich engines have the problem of the highly reactive preburned oxidizer gas wanting to burn anything it touches on its way and threatening the survival of turbines, pumps and ducts communicating that gas to the thrust chamber, regardless of the fuel used. The fixing in kerosene engines takes considerable amount of R&D work in fuel-rich case, and exotic oxidizer-compatible materials in oxidizer-rich case, both of which eventually drive the engine cost up. And even if these problems are fixed, it’s still impossible to source kerosene on Mars, or use it in long-duration deep space missions because it may freeze. We did not want these future factors to jeopardize the relevance of Centurion engines in the long run.
not hydrogen
Hydrogen will give 25% more thrust than kerosene or methane for the same amount of propellant flow into the engine. But hydrogen as a fuel does not have an industrial production base as mature and broad as kerosene or methane. It also needs to be stored on a rocket at extremely cold -420 degrees Fahrenheit! As cool as it sounds, it gives rise to countless needs: from intricate chilling and storage infrastructure on the ground, to the need to keep hydrogen from warming up or freezing the oxidizer to solid state on board of the rocket. Hydrogen results in large tanks and correspondingly large rockets due to its low density. It is also difficult to seal in plumbing components, like valves and ducts, due to its molecules being so small. These factors usually lead to hydrogen engines costing premium during their development, production and flight. Each Space Shuttle flight used to cost around $1B because of its expensive hydrogen architecture. The current Delta launches that are also based on hydrogen are not far behind that high cost either. Hydrogen is the most abundant substance in the universe, so it could potentially be sourced in deep space missions, but dealing with its ground and flight handling problems tilts the favorability balance toward methane.
What’s next in engine development?
The Centurion engine prototype is planned to undergo a thorough R&D hot-fire test campaign at the RPS test cell within 2023-2025 to demonstrate its performance at the component and system levels. Pending test results, we expect to transition to commercialization activities in Q1-Q2 of 2025. Please follow our updates to keep up with the latest results.